Material handling and transportation for raw materials & end products
Material handling is an essential part of many industrial processes in which bulk materials, powders, granules and liquids have to be efficiently moved, stored and processed. Techniques for handling materials in various forms: tank systems, silo systems, as well as innovative handling systems for containers such as IBCs, big bags, sacks, barrels or canisters. They enable efficient, safe and automated handling that is adapted to individual production requirements.


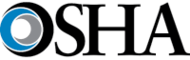