Service in plant engineering
IFA Technology offers you comprehensive technical support and after-sales service to keep your systems running optimally throughout their entire life cycle. Whether spare parts service, maintenance, training or control system conversions - we are your reliable partner for all services relating to your systems.


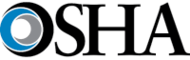